ADAS LiDAR
What is LiDAR?
LiDAR consists of a laser, a receiver and a processor, which can accurately illuminate the surface of any object in space, and one of the echoes must be reflected to the starting point and received by the receiver. The processor calculates the round-trip time of this light beam, and the precise distance of this point can be obtained. This ranging method is called “Time of Flight”, or TOF for short. The three-dimensional positioning of this point can be obtained by assigning angle information to this beam of light in the space coordinate system. When we have an infinite number of rays, we can use an infinite number of such points to outline the details of all objects in space, which is the “point cloud”- the three-dimensional vision of LiDAR. The performance of LiDAR is mainly reflected in its ranging capability, resolution and accuracy, which is a competition of the comprehensive strength of optical and electronic systems, and its reliability depends on the scanning module, which is a competition of mechanical design reliability.
LiDAR Classification
According to the structure, LiDAR can be divided into: mechanical, pure solid state, mixed solid state (rotating mirror and MEMS micro-galvo mirror).
Fully rotating mechanical LiDAR
The lasers with different emission angles are arranged longitudinally to form a vertical scanning line, and all the lasers are driven to rotate through the motor, and the 360-degree FOV (Field of View) is realized by lines. Although it satisfies the 360-degree full field of view coverage, due to the limitation of the angle and number of laser beams, the density of the point cloud (that is, the imaging effect of the object) will deteriorate as the distance increases. To increase the resolution and effective sensing distance, the only way to increase the wire beam is to increase the laser module, which leads to the continuous increase of the volume of the one-dimensional rotating mechanical radar, and the difficulty of aligning all the lasers in the process of installation and adjustment. rise. In order to take full advantage of the 360-degree field of view, autonomous vehicles have to install huge radars on the roof, which affects the aesthetics. Moreover, the high-frequency rotation and complex mechanical structure cause the average failure time to be only 1000-3000 hours, which is difficult to meet the minimum requirement of 13,000 hours for vehicle-grade equipment.
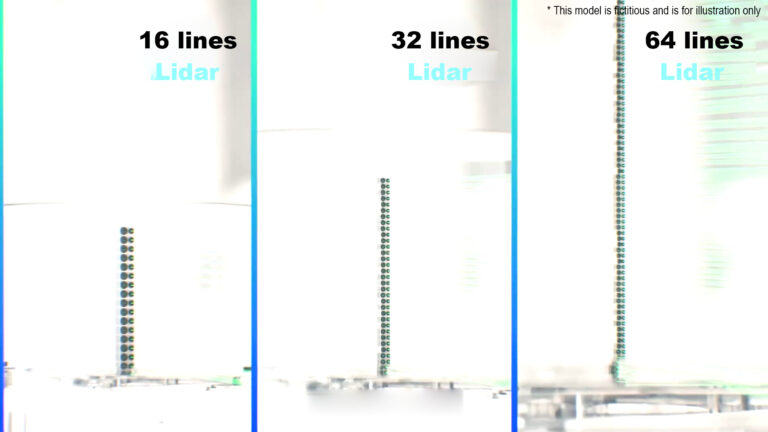
Pure solid-state LiDAR
Vehicle-grade equipment needs to work continuously in environments such as continuous vibration, high and low temperature, high humidity and high salt, etc., solid-state LiDAR has become a more feasible development direction. Compared to mechanical LiDAR, solid-state LiDAR only scans in one direction at a certain angle, and its coverage is limited. However, the mechanical structure of complex high-frequency rotation has been cancelled, the durability has been greatly improved, and the volume can be greatly reduced.
1)OPA Optical Phased Array
The principle is similar to the phased array radar carried on military aircraft and warships. By controlling the current phase of each element of the phased array radar plane array, the phase difference can make the wave sources in different positions interfere, so as to point in a specific direction. The effect of scanning can be achieved by reciprocating control of the phase difference. For device size, the material and process requirements are extremely demanding because of the high cost.
2) Flash LiDAR
The principle is similar to taking a photo. In a short period of time, a large area of laser light covering the detection area is directly launched forward, and the image of the surrounding environment is drawn through a highly sensitive receiver. However, since a large area of laser is emitted in a short period of time, the detection accuracy and detection distance will be greatly affected. It is mainly used for low-speed unmanned vehicles, such as unmanned food delivery vehicles, unmanned logistics vehicles, etc. In autonomous driving solutions that require less detection distance.
Hybrid solid-state LiDAR
Compared with mechanical LiDAR, hybrid solid-state LiDAR also only scans a range within a certain angle in front; and compared with pure solid-state LiDAR, hybrid solid-state LiDAR also has some smaller moving parts.
1)MEMS micro-galvanometer
The micron-scale galvanometer moves periodically at high speed in the horizontal and vertical axes through a thin cantilever beam, thereby changing the direction of laser reflection and realizing scanning. Because the receiver needs to capture enough light to achieve clear imaging at long distances, the micron-scale galvanometer cannot meet the ranging requirements of LiDAR. The aperture of ordinary LiDAR receivers is often around tens of millimeters, which leads to the continuous increase of the size of the galvanometer in the development of MEMS LiDAR, from the micron level to the centimeter level. However, the slender cantilever beam is facing the centimeter level for galvo mirrors, the lifespan issue has become a major unresolved challenge in the industry. In addition, the rotation angle of the cantilever beam is limited, resulting in a small field of view covered by a single galvanometer. Multiple splicing must be used to achieve a large field of view coverage, resulting in uneven distortion of the originally irregular point cloud image at the superimposed edge. And overlapping, better is not conducive to algorithm processing.
2)Rotating mirror
It is divided into one scanning mirror (one-dimensional rotating mirror) and one vertical and one horizontal two-sided scanning mirror (two-dimensional rotating mirror). The number of one-dimensional rotating mirrors is the same as the number of laser generators, while the two-dimensional rotating mirror can achieve more equivalent beams, which has advantages in integration difficulty and cost control.
- 2D Rotating Mirror – A scheme of local movement of two mirrors is adopted, which is the scanning core component of a semi-solid LiDAR. It consists of a polygonal prism that rotates continuously on the horizontal axis and a mirror that can swing on the vertical axis. The polygonal prism rotates continuously, which can make the light source scan horizontally on the target plane, while the vertical axis swing mirror continuously changes the vertical direction of the light source, so as to continuously change the emission direction of the light source, only one light source can complete the mechanical radar with several light sources. Completed scan task. But a beam of light source needs a very high scan rate to complete the full-plane scan. What a mechanical radar can accomplish in just 10 rotations requires hundreds of thousands of rotations for a mirror.
- One-dimensional rotating mirror – Using a mirror that only rotates at a low speed in the horizontal direction, and stacks more laser channels in the vertical direction, but if the traditional discrete device design is still used, it will bring problems such as very large volume and skyrocketing cost. And the ultimate answer to all these problems is microchips.
3)Corner
Prism LiDAR is also called double wedge prism LiDAR, which includes two wedge prisms inside, the laser is deflected once after passing through the first wedge prism, and deflected again after passing through the second wedge prism. The scanning shape of the laser beam can be controlled by controlling the relative rotation speed of the two prisms.
LiDAR Applications
SINO-GALVO solution for LiDAR
Galvo scanner for 2D Rotating Mirror LiDAR
How to choose the laser wavelength for LiDAR?
Wavelength | Advantages | Disadvantages |
---|---|---|
905nm lidar | Lower cost | Limitation of detection distance |
1550nm lidar | Longer detection distance | Higher cost |
ADAS LiDAR
What is LiDAR?
LiDAR consists of a laser, a receiver and a processor, which can accurately illuminate the surface of any object in space, and one of the echoes must be reflected to the starting point and received by the receiver. The processor calculates the round-trip time of this light beam, and the precise distance of this point can be obtained. This ranging method is called “Time of Flight”, or TOF for short. The three-dimensional positioning of this point can be obtained by assigning angle information to this beam of light in the space coordinate system. When we have an infinite number of rays, we can use an infinite number of such points to outline the details of all objects in space, which is the “point cloud”- the three-dimensional vision of LiDAR. The performance of LiDAR is mainly reflected in its ranging capability, resolution and accuracy, which is a competition of the comprehensive strength of optical and electronic systems, and its reliability depends on the scanning module, which is a competition of mechanical design reliability.
LiDAR Classification
According to the structure, LiDAR can be divided into: mechanical, pure solid state, mixed solid state (rotating mirror and MEMS micro-galvo mirror).
Fully rotating mechanical LiDAR
The lasers with different emission angles are arranged longitudinally to form a vertical scanning line, and all the lasers are driven to rotate through the motor, and the 360-degree FOV (Field of View) is realized by lines. Although it satisfies the 360-degree full field of view coverage, due to the limitation of the angle and number of laser beams, the density of the point cloud (that is, the imaging effect of the object) will deteriorate as the distance increases. To increase the resolution and effective sensing distance, the only way to increase the wire beam is to increase the laser module, which leads to the continuous increase of the volume of the one-dimensional rotating mechanical radar, and the difficulty of aligning all the lasers in the process of installation and adjustment. rise. In order to take full advantage of the 360-degree field of view, autonomous vehicles have to install huge radars on the roof, which affects the aesthetics. Moreover, the high-frequency rotation and complex mechanical structure cause the average failure time to be only 1000-3000 hours, which is difficult to meet the minimum requirement of 13,000 hours for vehicle-grade equipment.
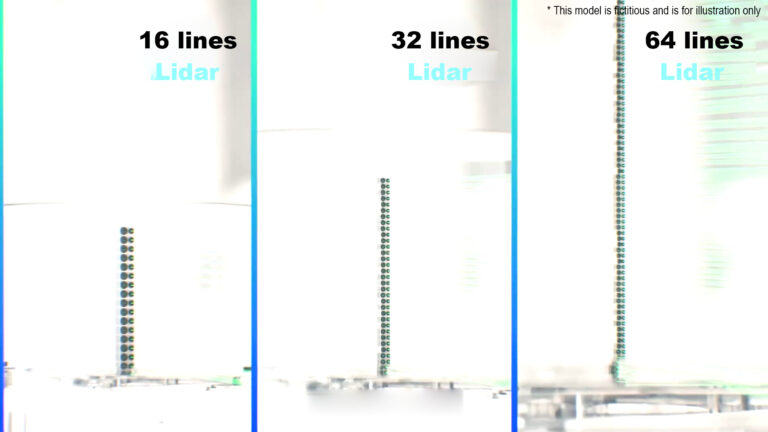
Pure solid-state LiDAR
Vehicle-grade equipment needs to work continuously in environments such as continuous vibration, high and low temperature, high humidity and high salt, etc., solid-state LiDAR has become a more feasible development direction. Compared to mechanical LiDAR, solid-state LiDAR only scans in one direction at a certain angle, and its coverage is limited. However, the mechanical structure of complex high-frequency rotation has been cancelled, the durability has been greatly improved, and the volume can be greatly reduced.
1)OPA Optical Phased Array
The principle is similar to the phased array radar carried on military aircraft and warships. By controlling the current phase of each element of the phased array radar plane array, the phase difference can make the wave sources in different positions interfere, so as to point in a specific direction. The effect of scanning can be achieved by reciprocating control of the phase difference. For device size, the material and process requirements are extremely demanding because of the high cost.
2) Flash LiDAR
The principle is similar to taking a photo. In a short period of time, a large area of laser light covering the detection area is directly launched forward, and the image of the surrounding environment is drawn through a highly sensitive receiver. However, since a large area of laser is emitted in a short period of time, the detection accuracy and detection distance will be greatly affected. It is mainly used for low-speed unmanned vehicles, such as unmanned food delivery vehicles, unmanned logistics vehicles, etc. In autonomous driving solutions that require less detection distance.
Hybrid solid-state LiDAR
Compared with mechanical LiDAR, hybrid solid-state LiDAR also only scans a range within a certain angle in front; and compared with pure solid-state LiDAR, hybrid solid-state LiDAR also has some smaller moving parts.
1)MEMS micro-galvanometer
The micron-scale galvanometer moves periodically at high speed in the horizontal and vertical axes through a thin cantilever beam, thereby changing the direction of laser reflection and realizing scanning. Because the receiver needs to capture enough light to achieve clear imaging at long distances, the micron-scale galvanometer cannot meet the ranging requirements of LiDAR. The aperture of ordinary LiDAR receivers is often around tens of millimeters, which leads to the continuous increase of the size of the galvanometer in the development of MEMS LiDAR, from the micron level to the centimeter level. However, the slender cantilever beam is facing the centimeter level for galvo mirrors, the lifespan issue has become a major unresolved challenge in the industry. In addition, the rotation angle of the cantilever beam is limited, resulting in a small field of view covered by a single galvanometer. Multiple splicing must be used to achieve a large field of view coverage, resulting in uneven distortion of the originally irregular point cloud image at the superimposed edge. And overlapping, better is not conducive to algorithm processing.
2)Rotating mirror
It is divided into one scanning mirror (one-dimensional rotating mirror) and one vertical and one horizontal two-sided scanning mirror (two-dimensional rotating mirror). The number of one-dimensional rotating mirrors is the same as the number of laser generators, while the two-dimensional rotating mirror can achieve more equivalent beams, which has advantages in integration difficulty and cost control.
- 2D Rotating Mirror – A scheme of local movement of two mirrors is adopted, which is the scanning core component of a semi-solid LiDAR. It consists of a polygonal prism that rotates continuously on the horizontal axis and a mirror that can swing on the vertical axis. The polygonal prism rotates continuously, which can make the light source scan horizontally on the target plane, while the vertical axis swing mirror continuously changes the vertical direction of the light source, so as to continuously change the emission direction of the light source, only one light source can complete the mechanical radar with several light sources. Completed scan task. But a beam of light source needs a very high scan rate to complete the full-plane scan. What a mechanical radar can accomplish in just 10 rotations requires hundreds of thousands of rotations for a mirror.
- One-dimensional rotating mirror – Using a mirror that only rotates at a low speed in the horizontal direction, and stacks more laser channels in the vertical direction, but if the traditional discrete device design is still used, it will bring problems such as very large volume and skyrocketing cost. And the ultimate answer to all these problems is microchips.
3)Corner
Prism LiDAR is also called double wedge prism LiDAR, which includes two wedge prisms inside, the laser is deflected once after passing through the first wedge prism, and deflected again after passing through the second wedge prism. The scanning shape of the laser beam can be controlled by controlling the relative rotation speed of the two prisms.
LiDAR Applications
SINO-GALVO solution for LiDAR
Galvo scanner for 2D Rotating Mirror LiDAR
How to choose the laser wavelength for LiDAR?
Wavelength | Advantages | Disadvantages |
---|---|---|
905nm lidar | Lower cost | Limitation of detection distance |
1550nm lidar | Longer detection distance | Higher cost |