Among metal materials, laser processing of steel has become mature, while the processing of highly reflective materials is still being explored, especially copper and aluminum materials. Because of its excellent electrical and thermal conductivity and its lower price than gold and silver, copper is widely used in manufacturing fields such as electronic products and electric vehicles, as well as motors, batteries, sensors, wiring harnesses, and terminals. As copper materials become more and more widely used, high-reliability welding and connection of copper become more and more important.
Since the thermal conductivity of copper is almost 5 times of pure iron and 1.7 times of pure aluminum, the traditional arc welding method is not ideal because of lower power density and bad welding effect. Laser welding has the characteristics of high-power density, fast welding speed, and small welding heat impact, which is considered a suitable process for copper connections.
760nm~1mm Infrared laser of Copper welding
The most common laser for material processing applications is infrared laser with a wavelength between 760nm and 1mm, and its frequency is between microwave and visible light. However, infrared laser for copper processing has the following disadvantages:
- The absorption rate of infrared laser by solid copper is only 3%~5%, making it difficult to form a stable molten pool at the initial stage of welding. It is prone to defects such as spatter, melt ejection and holes.
- The reflectivity of copper is as high as 90%, so high power is needed to overcome the reflection problem of the material and ensure that enough material is transmitted to the copper. However, high-power laser will cause the copper material to be easily deformed, and even if the processing and welding are completed, defects and missed welding will easily occur.
- Due to the good thermal conductivity of copper, once it is locally heated, the heat diffuses rapidly and it is not easy to accumulate heat to achieve the processing effect.
532nm Green Laser of Copper welding
The reflectivity of 532nm laser for welding copper materials is much lower than that of 1064nm laser, only 45%. The effect is as good as the welding results of 1064 nm laser on steel materials.
450nm Blue laser of Copper welding
Since green lasers with wavelengths of 515nm and 532nm rely on their nonlinear optical crystals to convert the pump laser energy into energy at the target wavelength, the conversion process will result in higher power loss, and the lasers require complex cooling systems and complex optical settings., lasers are expensive and inefficient. The blue laser semiconductor laser based on gallium nitride material can directly generate laser with a wavelength of 450nm without further frequency doubling. It has the advantages of simple structure, easy to use, high electro-optical conversion efficiency, and high absorption rate. Its main advantages are as follows:
- The absorption rate of blue laser on copper materials is better than green laser, up to about 65%, which is 13 times of infrared laser, and the reflectivity can be reduced to less than 35%.
- Blue laser welding can be used in both heat conduction welding and deep penetration welding, both of which can achieve “spatter-free welding” and reduce missing welding pores.
- Blue laser welding of copper metal also has obvious speed advantages, at least 5 times faster than infrared laser welding. For example, the effect of using 500W blue laser is similar to 3000W infrared laser, which greatly saves energy and electricity waste.
Currently, the visible lasers have lower power and brightness, are mainly suitable for welding less than 0.5mm thick copper plates. To achieve better copper welding effects, double-beam hybrid welding (using blue laser beam and infrared laser beam to simultaneously weld copper materials) can be considered, which could solve high reflection issue and could achieve sufficient energy density. In summary, for brass welding, dual-beam composite welding > blue laser > green laser > infrared laser.
Galvanometer scanner and laser welding head are important components of welding equipment. Sino-galvo is specialized in development of galvanometer scanners, could provide welding solutions in various wavelength.
Playlist

0:16
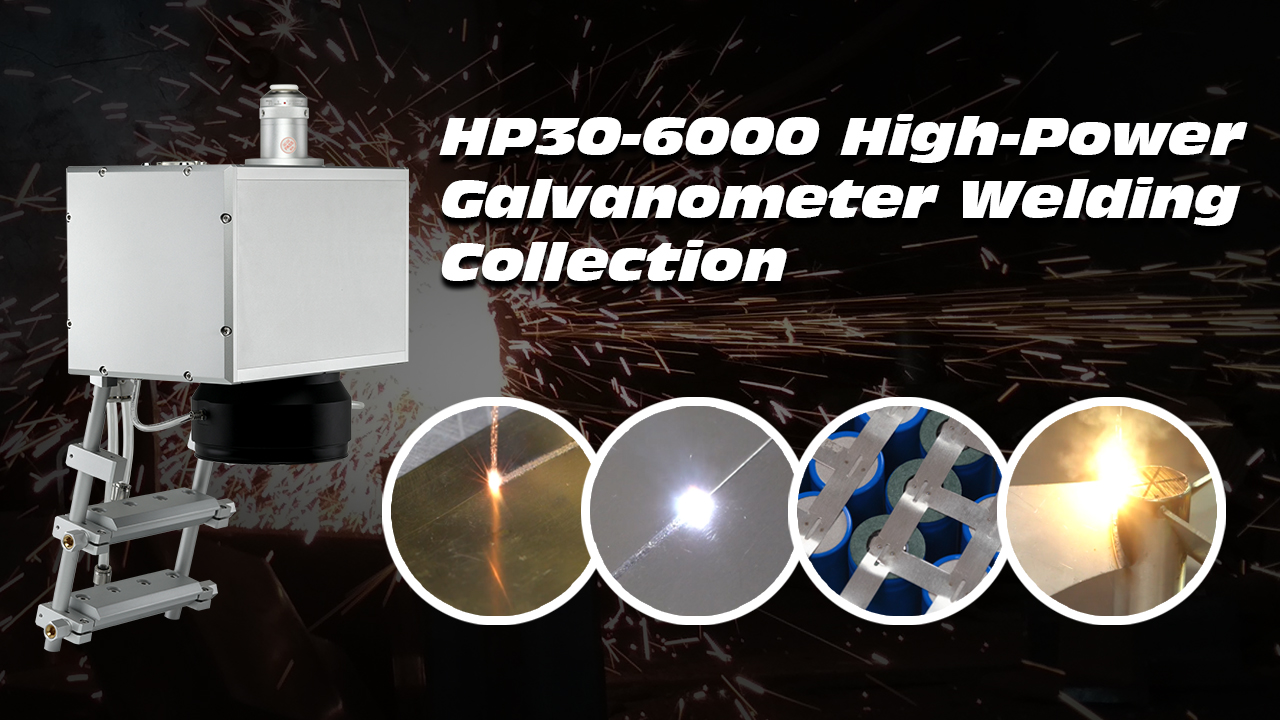
0:16
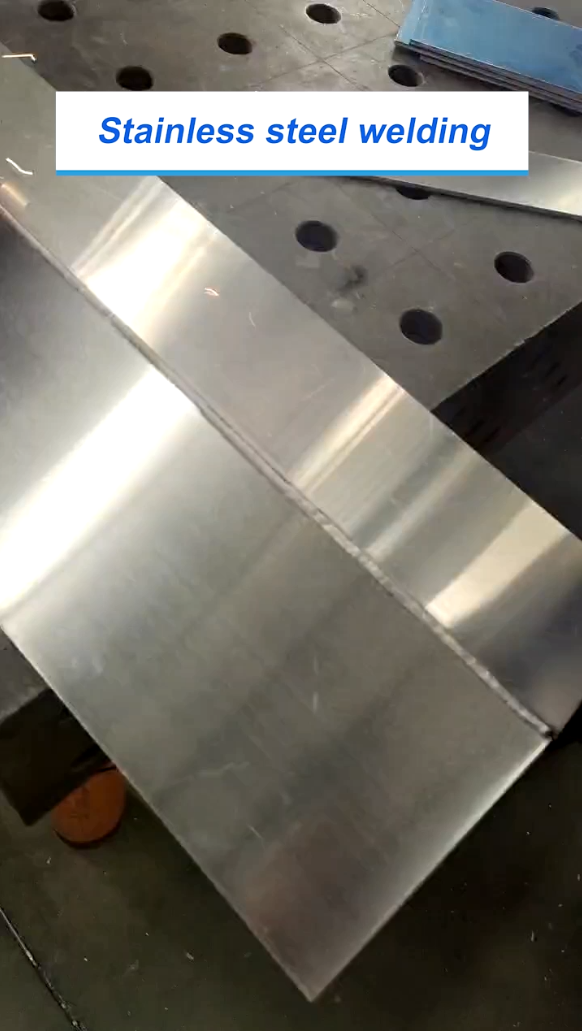
0:16
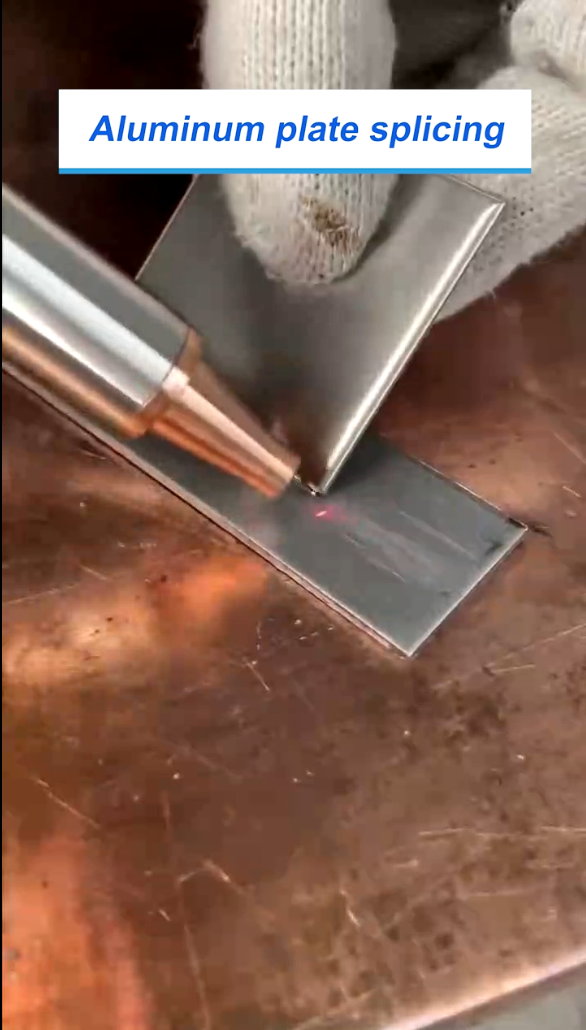